Testen und Prüfen von hochsensibler Mikroelektronik
Wir sind spezialisiert auf die anspruchsvolle Qualitätssicherung von elektrostatisch empfindlichen Baugruppen und Geräten und testen und justieren komplexe Baugruppen und elektrostatisch empfindliche Geräte mit dauerhaft höchster Präzision und Zuverlässigkeit.
Testen von elektromechanischen Baugruppen
Fachmännisch routiniert in der anspruchsvollen medizintechnischen Qualitätssicherung, führen unsere qualifizierten Mitarbeiter:innen Funktions-, Last- und Endprüfung von komplexen Baugruppen und hochsensiblen Baukomponenten wie Sensoren oder Platinen mit höchster Präzision und Zuverlässigkeit durch.
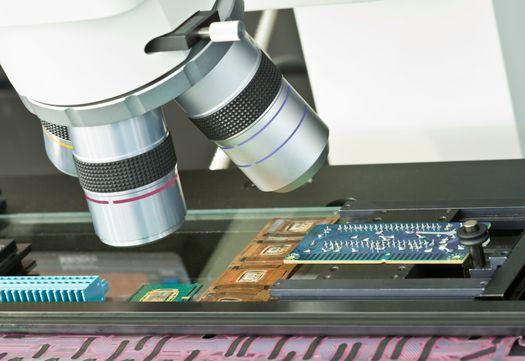
Function Testing
Der Zweck des Funktionstests (Function Test) ist es, die grundsätzliche Funktion aller Elektronikkomponenten sowie deren Zusammenspiel systematisch zu prüfen und dauerhaft sicherzustellen.
Mit Hilfe des Funktionstests prüft CrossTEQ systematisch und zuverlässig die Gesamt- oder Teilfunktion einer Baugruppe oder eines ganzen Systems. Der Funktionstest beinhaltet dabei sowohl die Endprüfung nach Fertigung einer Baugruppe als auch nach dem Einbau der jeweiligen Baugruppe im fertigen Gerät.
Anwendungsbeispiel:
Funktionstest eines großflächigen, hochsensiblen Bildsensors bei der Wareneingangskontrolle
Bei diesem Funktionstest testen wir die Aufnahme von Röntgenbildern in der Dunkelkammer, mit dem Ziel, dabei Fehler zu entdecken, die durch das Zusammenspiel der Komponenten verursacht werden.
Bei der Warenannanhme solcher Panels werden zuerst Arbeitsplatz und Vorrichtungen mit ionisierter Druckluft gereinigt und die Geräteerdung sichergestellt. Vor dem eigentlichen Panel-Funktionstest wird zuerst die Vakuums-Handlingsvorrichtung geprüft. Dafür wird der Bildsensor mit der Vorrichtung aus der Verpackung entnommen und in Bildsensor Testvorrichtung eingelegt. Nachdem der Bildsensor in die Testvorrichtung eingelegt wurde, wird dieser sauber an den PCBs ausgerichtet und alle Flexkabel in Klemmen eingesteckt und geschlossen. Der Bildsensor wird möglichst lichtdicht abgedeckt, wenn er an die Teststation angeschlossen und die Prüfung durchgeführt wird.
Burn-in Testing
Mit einer Belastungsschnellprüfung (auch Burn-in Test genannt) soll die Grenzlast von Komponenten, Baugruppen oder Komplettgeräten im Dauerbetrieb ermittelt werden. Bei CrossTEQ wird die Belastbarkeit beim Burn-In Test unter extremen Bedingungen, wie hoher Betriebsfrequenz oder Stromspannung während 48 Stunden ohne Unterbruch getestet.
Ziel des Burn-In Tests ist es, vor Anlauf der Massenproduktion Teile zu identifizieren, die verfrüht (vor der Nennlebensdauer) ausfallen könnten.
Anwendungsbeispiel:
Regelmässige Aufnahme von Dunkelfeldbildern und Erzeugung von Driftbildern mit Röntgentherapie-Imager
Bei diesem Burn-in Test prüft CrossTEQ einen komplett montierten Strahlentherapie-Imager über eine Dauer von 48 Stunden. Dabei werden in regelmäßigen Abständen Dunkelfeldbilder aufgenommen und Driftbilder erzeugt.
Ziel ist es, frühzeitige Ausfälle von Komponenten zu erkennen und das Fehlerpotenzial im Feld zu reduzieren. Die Bilder werden von der Testsoftware ausgewertet, die aus basierend darauf den Testbericht erstellt. Nach einer einminütigen Wartezeit zum Aufwärmen des Imagers werden die ersten beiden Bilder angefordert und verarbeitet. Das Driftbild und der mittlere Driftwert werden angezeigt.
Factory Acceptance Test (FAT)
Mit Hilfe des Factory Acceptance Tests (auch Endabnahmetest oder Werksabnahmeprüfung genannt) wird überprüft, ob die gefertigte Baugruppe bzw. das fertige Gerät den vorgesehenen Zweck erfüllt. Der FAT validiert den Betrieb der Geräte und stellt sicher, dass die Bestellspezifikationen des Kunden und alle anderen Anforderungen erfüllt wurden.
Anwendungsbeispiel:
Endabnahmetest (Röntgentest) zur Aufnahme von Röntgentestbildern mit Radiotherapie-Imagers
Bei diesem FAT handelt es sich um einen in Zusammenarbeit mit dem Kunden erarbeitete n Röntgentest zur Aufnahme von Röntgentestbildern mit Radiotherapie-Imagers.
Dabei werden in einer spezifisch dafür gefertigten Röntgenkammer sowohl automatische als auch manuelle visuelle Testschritte durchgeführt, um die Bildqualität des Imagers zu bestimmen. Ziel ist es, Fehler zu finden, die durch das Zusammenspiel der Komponenten verursacht werden.
Error rate 2021
Error detection rate 2021
CrossTEQ complies with all ISO 9001 standard requirements and is committed to their practical implementation in all areas of the company. Thus, each manufactured system, or subsystem is subject to strict quality monitoring by our qualified and regularly trained staff. Only after the inspection is successful, the assembly of the module or device is completed.
Dank komplett digitalisierten Fertigungsprozessen gewährleisten wir höchste Prozesssicherheit und Qualität auf dem neuesten Stand der Technik.
Dadurch erkennen wir Fehler und Risiken schneller und können Abweichungen lückenlos zurückführen;
Andererseits können wir so die Rückverfolgbarkeit aller verwendeten Materialien und Komponenten gewährleisten.
Test requirements and test instructions
CrossTEQ sorgt dafür, dass das Personal in der Durchführung von Tests angemessen geschult ist. Nur regelmäßig geschultes Produktionspersonal, darf Tests durchführen.
Unser Qualitätspersonal (Produktionsleiter und Leiter der Fertigungstechnik) pflegt und implementiert Arbeitsanweisungen, Richtlinien zur Testumgebung sowie allfällige Vorsichtsmaßnahmen (insbesondere für elektrostatisch empfindliche Geräte!).
Die Testanwendungssoftware führt den Tester durch die verschiedenen Testschritte und führt den automatisierten Testabschnitt aus, wo dies möglich ist. Die Testanwendung dokumentiert und erstellt digitale Testberichte, welcher der Tester unterschreiben muss.
Abweichungen/Mängel werden auf dem Prüfbericht vermerkt. Etwaige Korrekturmaßnahmen und die folgenden Regressionstests werden detailliert beschrieben.
Gemäss der Liefervereinbarung archiviert CrossTEQ Berichte als Teil des Device History Record (DHR). Jeder Bericht ist anhand der Teile-Identifikationsnummer und der Seriennummer auf das Bauteil rückführbar.
Unser Qualitätspersonal führt den Quality Assurance (QA) Buyoff für die Produktfreigabe durch und bestätigt die ordnungsgemäße Herstellung, Prüfung und Berichterstattung durch elektronische Unterzeichnung, bevor an den Kunden geliefert wird.
Wir sind spezialisiert auf die anspruchsvolle Qualitätssicherung von elektrostatisch empfindlichen Baugruppen und Geräten.
Gerne montieren, testen und justieren wir Ihre komplexen Baugruppen und hochsensible Mikroelektronik mit dauerhaft höchster Präzision und Zuverlässigkeit.
Ihre Vorteile mit CrossAssembly Services von CrossTEQ
Ihre Liefertreue steht und fällt mit der Endmontage: Experten sind gefragt! Sichern Sie sich jetzt Ihre eigene Reaktivität und überlassen Sie unseren Montage-Experten die Verantwortung über diese letzte, wichtige Etappe der Produktentstehung.
Streamlining processes
Durch die Auslagerung Ihrer Baugruppenmontage und anderen Aufgaben und Produktionsprozessen an uns, verschlanken Sie Ihr eigenes Unternehmen und bleiben agil.
Save resources
Indem Sie uns mit der Montage Ihrer Baugruppen beauftragen, sparen Sie eigene Ressourcen bei Personal, Infrastruktur und Technologie und können diese stattdessen effizienter an internen Schlüsselstellen einsetzen.
Pragmatic and efficient
Bei CrossTEQ pflegen wir eine dynamische Personal- und Produktionsplanung, effiziente Fertigungsprozesse und kurze Kommunikationswege sowohl mit unseren Kunden als auch mit unseren, bzw. Ihren Lieferanten.
Maximum reactive and flexible
Wir bauen auf sichere Quellen und verhältnismässige Reserven und Redundanz bei der Material- und Personalplanung, um auch bei kurzfristigen Montage-Aufträgen termin- und qualitätsgerecht an Sie liefern zu können.