Best Practices in der Faserverbundtechnik
Design, Fertigung und Prozessoptimierung
Einleitung
Die Faserverbundtechnik ist eine der fortschrittlichsten Technologien im Bereich moderner
Werkstoffe. Sie bietet einzigartige Vorteile wie hohe Festigkeit, geringes Gewicht und
hervorragende Korrosionsbeständigkeit. Doch die Nutzung dieser Werkstoffe erfordert ein
fundiertes Verständnis der Designrichtlinien, Fertigungstechniken und
Prozessoptimierungen. Dieser Leitfaden bietet Technikerinnen und Technikern einen
umfassenden Überblick über bewährte Verfahren und Best Practices in der
Faserverbundtechnik.
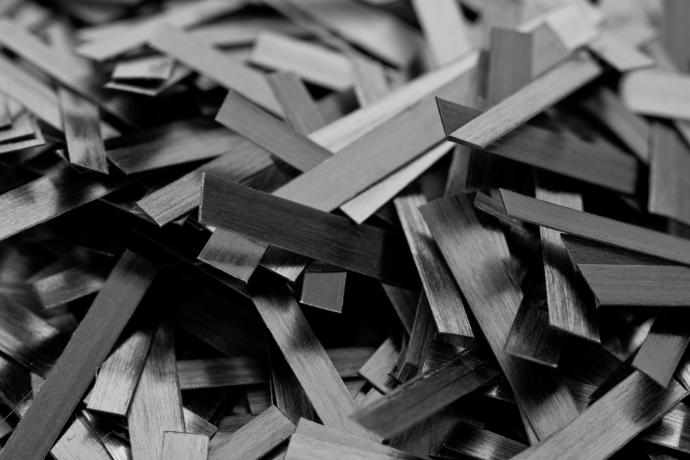
Design Guidelines: Richtig konstruieren mit Faserverbundwerkstoffen
1. Grundprinzipien des Designs
Lastpfadoptimierung
- Faserverbundwerkstoffe sind anisotrop, das heißt, ihre Eigenschaften variieren je nach Richtung. Entwerfen Sie Bauteile so, dass die Fasern in die Hauptlastrichtung orientiert sind, um maximale Festigkeit und Steifigkeit zu erreichen.
- In multidirektional belasteten Bereichen sollten Sie hybride Layups verwenden, um eine gleichmäßige Lastverteilung sicherzustellen.
- Lastpfadoptimierung hilft dabei, Material effizient einzusetzen und das Bauteilgewicht zu minimieren, was insbesondere in der Luft- und Raumfahrt oder Automobilindustrie von Vorteil ist.
Schichtaufbau (Laminatdesign)
- Der Schichtaufbau beeinflusst direkt die mechanischen Eigenschaften des Laminats. Eine ausgewogene Laminatstruktur, wie [0°/90°] oder [+45°/-45°], reduziert Verzug und Delamination.
- Stellen Sie sicher, dass jede Schicht ausreichend an die benachbarten Schichten gekoppelt ist, um Schubversagen zu vermeiden.
- Für Anwendungen mit hohen dynamischen Belastungen sollten Sie Layups mit erhöhter Zähigkeit in Betracht ziehen, um Ermüdungsrisse zu minimieren.
Vermeidung von Spannungskonzentrationen
- Abrupte Querschnittsänderungen und scharfe Kanten sollten vermieden werden, da sie zu lokalen Spannungsspitzen führen können. Verwenden Sie stattdessen Radien und glatte Übergänge, um die Belastung gleichmäßig zu verteilen.
- Bei Befestigungen und Durchbrüchen, wie Schraublöchern oder Aussparungen, sollten Verstärkungen eingebracht werden, um das Risiko von Rissbildung oder Delamination zu reduzieren.
Sandwich-Konstruktionen
- Diese Konstruktionen kombinieren leichte Kerne, wie Waben- oder Schaummaterialien, mit hochfesten Deckschichten. Dadurch wird die Biegesteifigkeit erheblich verbessert, ohne das Gewicht zu erhöhen.
- Achten Sie darauf, dass der Kern und die Deckschichten kompatibel sind, um Schäden durch unterschiedliche thermische Ausdehnungskoeffizienten zu vermeiden.
- Für strukturelle Anwendungen, wie Flugzeugtragflächen oder Fahrzeugkarosserien, bieten Sandwichkonstruktionen eine optimale Kombination aus Festigkeit und Gewichtseffizienz.
2. Materialauswahl
Fasertypen
Glasfaser
Kostengünstig, gute Festigkeit, hohe Schlagzähigkeit.
Carbonfaser
Hervorragendes Festigkeits-Gewichts-Verhältnis, jedoch teuer.
Aramidfaser (Kevlar)
Hohe Schlagzähigkeit, geringe Druckfestigkeit.
Matrixmaterialien
Thermoplaste
Wiederverwendbar, gute Zähigkeit.
Duroplaste
Hohe Temperatur- und chemische Beständigkeit, jedoch schwer zu
recyceln.
3. CAD und Simulation
FEM-Analyse (Finite-Elemente-Methode)
- Simulieren Sie Belastungen, Verformungen und Spannungen im Bauteil.
- Identifizieren Sie Schwachstellen und optimieren Sie die Faserorientierung.
Topologieoptimierung
- Reduzieren Sie Materialverbrauch und Gewicht, indem Sie Strukturen gezielt an Belastungen anpassen.
Fertigungshinweise: Vom Entwurf zur Realität
1. Fertigungsverfahren – Worauf zu achten ist
Autoklavverfahren
- Verwenden Sie präzise Temperatur- und Druckprofile, um ein gleichmäßiges Aushärten der Harzmatrix zu gewährleisten.
- Sorgen Sie für eine ausreichende Entlüftung, um Lufteinschlüsse und Porosität zu vermeiden.
- Regelmäßige Wartung des Autoklaven ist erforderlich, um Temperaturschwankungen zu minimieren.
Resin Transfer Molding (RTM)
- Stellen Sie sicher, dass die Form luftdicht ist, um eine effiziente Harzinjektion zu gewährleisten.
- Wählen Sie das richtige Harz mit niedriger Viskosität, um die Fließeigenschaften zu optimieren.
- Überwachen Sie die Aushärtezeit genau, um Delaminationen zu vermeiden.
Compression Molding
- Verwenden Sie vorgefertigte Preforms, um Materialverluste zu minimieren.
- Stellen Sie sicher, dass die Temperatur des Werkzeugs gleichmäßig verteilt ist.
- Reinigen Sie die Formen nach jedem Zyklus, um Oberflächenfehler zu verhindern.
3D-Druck
- Achten Sie auf die richtige Kombination aus Faser- und Matrixmaterial, um die mechanischen Eigenschaften zu maximieren.
- Optimieren Sie die Schichthöhe und -ausrichtung, um die Festigkeit des Bauteils zu verbessern.
- Verwenden Sie Druckparameter, die auf das spezifische Material abgestimmt sind.
2. Prozesskontrolle
Temperaturüberwachung
- Präzise Steuerung der Aushärtetemperatur, um Materialfehler zu vermeiden.
Vakuumtechnologie
- Entfernen Sie alle Lufteinschlüsse, um eine einheitliche Harzverteilung zu gewährleisten.
Qualitätssicherung
- Regelmäßige zerstörungsfreie Prüfungen (z. B. Ultraschall oder Thermografie) zur Früherkennung von Fehlern.
3. Nachhaltigkeit in der Fertigung
Recycling
- Einsatz thermoplastischer Matrizes für wiederverwendbare Verbundwerkstoffe.
Energieeffizienz
- Optimierung der Aushärtezyklen zur Reduktion des Energieverbrauchs.
Prozessoptimierung und Best Practices
1. Fehlervermeidung
Delamination
Ursachen:
- Unsachgemäße Laminatschichtung mit falscher Faserorientierung oder ungleichmäßiger Harzverteilung.
- Mechanische Überlastung oder thermische Spannungen durch fehlerhafte Aushärtezyklen.
Auftreten:
- An Schichtgrenzen oder in Bereichen mit hohen Kräften wie Ecken oder Kanten.
Porosität
Ursachen:
- Lufteinschlüsse durch unzureichende Vakuumanwendung oder hohe Harzviskosität.
- Unkontrollierte Temperatur- oder Druckschwankungen.
Auftreten:
- Im gesamten Laminat, besonders bei dickeren Strukturen oder großflächigen Bauteilen.
Faserwelligkeit (Fiber Wrinkling)
Ursachen:
- Schlechte Faserplatzierung oder Überdruck während des Harzeinbringens.
- Unsachgemäßer Schichtaufbau, insbesondere bei komplexen Geometrien.
Auftreten:
- An Stellen mit starker Krümmung oder in dickeren Laminaten.
2. Effizienzsteigerung
Automatisierung
- Nutzen Sie automatisierte Faserlegeverfahren (AFP, ATL) für gleichbleibende Qualität und Geschwindigkeit.
Prozessintegration
- Kombinieren Sie Schritte wie Schneiden, Faserlegen und Aushärten in einem Produktionsablauf.
3. Schulung und Weiterbildung
Wissenstransfer
- Regelmäßige Schulungen für Fertigungspersonal zu neuen Materialien und Verfahren.
Technologietraining
- Anwendung neuer Softwaretools für Simulation und Prozessüberwachung.
Fazit
Die erfolgreiche Anwendung von Faserverbundwerkstoffen hängt von der Beherrschung moderner Designrichtlinien, Fertigungsmethoden und Prozessoptimierungen ab. Durch die Einhaltung dieser Best Practices können Technikerinnen und Techniker die Vorteile dieser innovativen Materialien voll ausschöpfen und gleichzeitig Fehler und Ineffizienzen minimieren.
Bleiben Sie wettbewerbsfähig, indem Sie Ihre Kenntnisse in der Faserverbundtechnik kontinuierlich erweitern und die neuesten Technologien nutzen. Kontaktieren Sie uns für weitere Informationen oder Schulungen zu Best Practices in der Faserverbundtechnik.
Bleiben Sie wettbewerbsfähig, indem Sie Ihre Kenntnisse in der Faserverbundtechnik kontinuierlich erweitern.
Kontaktieren Sie uns für weitere Informationen oder Schulungen zu Best Practices in der Faserverbundtechnik.