ACF-Heat Seal Bonding
Unsere Montage-Experten sind spezialisiert im ACF-Heat Sealing von Elektronikkomponenten an empfindliche Sensor-Panels. Kontaktieren Sie uns bei Fragen zur HSB-Verbindungstechnik oder Ihren Möglichkeiten mit dem ACF-Heat Seal Bonding-Verfahren von CrossTEQ.
ACF-HSB Verfahren für die Herstellung von grossen Bildsensoren
In Zusammenarbeit mit unserem Partner Getronic Engineering AG hat CrossTEQ ein spezifisches, halbautomatisches ACF-Heat Seal Bonding Verfahren für die Herstellung von hochsensiblen, grossflächigen Röntgenbildsensor-Panels in der Medizinaltechnik mitentwickelt. Beim entwickelten Prozess werden flexible Leiterplatten (Flex PCBs) mit einem Leiterabstand von lediglich 0.150mm und einer Leiterbreite von nur 0.100mm auf eine auf amorphem Silikon basierende Basisplatte kontaktiert.
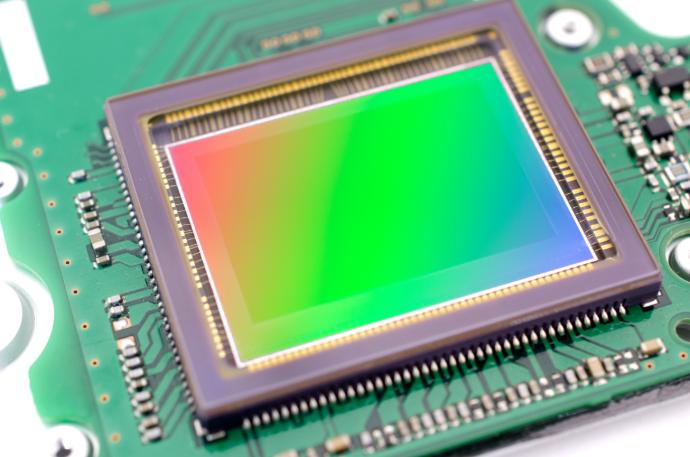
Was ist die ACF-Heat Seal Bonding Verbindungstechnik
Anisotropes leitfähiges Kleben (kurz ACF-HSB für Anisotropic Conductive Film Heat Seal Bonding) ist eine Verbindungstechnik, zur stoffschlüssigen und präzisen Kontaktierung von flexiblen Leiterbahnen an ein Basismedium, wie z.B ein LCD-Panel. Durch die Verwendung von Flex-Folien und anisotropem leitfähigem Klebstoff (bei dem die elektromagnetischen Eigenschaften von der Richtung abhängen, während bei isotropen Materialien hingegegen die elektromagnetischen Eigenschaften in alle Richtungen gleich sind) können durch ACF-Heat Seal Bonding nahezu alle Materialien optisch ansprechend gefügt und eine gleichmäßige Verteilung der Klebekraft ohne Wärmebelastung oder Beeinträchtigungen des Werkstoffs erreicht werden.
Das sind die Verbindungseigenschaften von ACF-HSB vs. HSC
Heatseal-Verbindungen haben einen relativ hohen Widerstand und eine geringe maximale Stromdichte. Der elektrische Widerstand liegt im Bereich von 2-10 Ω für PCB-Verbindungen und 10-100 Ω für LCD-Verbindungen. Der Isolationswiderstand liegt im Bereich von 109 bis 10 10 Ω Bereich. ACF kann Temperaturen bis zu +80 bis +120 °C standhalten während bei HSC der effektive Temperaturvergleich bei -40 bis +60 °C liegt.
Sie haben Fragen zur HSB-Verbindungstechnik oder Ihren Möglichkeiten mit dem ACF-Heat Seal Bonding-Verfahren von CrossTEQ?
Wir sind spezialisiert im ACF-Heat Sealing von Elektronikkomponenten an empfindliche Sensor-Panels und helfen Ihnen gerne weiter. Kontaktieren Sie uns!
Wieso ACF-Heat Sealing?
Anisotropes leitfähiges (ACF) Heat Seal Bonding weist eine äusserst hohe Verbindungsqualität auf, weswegen in der Fertigungsindustrie eine starke Verlagerung hin zu dieser Verbindungstechnik stattfindet. Die explosionsartige Zunahme der Nutzung von Displays, sowie neue Entwicklungen in der Produktionstechnik, wie Vision-gestützte automatische Ausrichtung und vollautomatische Anisotropic Conductive Foil Module haben kürzlich den Weg für eine breite Anwendung dieser Technik geebnet.
ACF-HSB Prozess
Vor der Verbindung trennt ein isolierender Klebefilm die leitfähigen Partikel. Wenn ein Heizelement die obere und untere Leiterplatte mit dem dazwischen liegenden Klebstoff zusammenpresst, fließt der Klebstoff und die leitenden Partikel werden eingeschlossen, was zu einer elektrischen Verbindung führt.
Bei anisotropischem Heat Sealing erfolgt die Kompression nur in Richtung der Z-Achse, weshalb eine elektrische Verbindung nur in dieser Richtung hergestellt. Aufgrund des geringen Füllstoffgehalts (1-5 %) kann ein Kurzschluss zwischen benachbarten Leiterbahnen nicht stattfinden.
Der Klebstoff besteht normalerweise aus einer Mischung aus thermoplastischen und thermohärtenden (auch bekannt als duroplastischen) Klebstoffen, um das Beste aus beiden Eigenschaften zu erhalten. Thermisch härtende Kleber benötigen eine höhere Temperatur und eine längere Aushärtezeit als thermoplastische Klebstoffe. Aufgrund ihrer höheren Schmelztemperatur benötigt, wird dafür am häufigsten Polyamidfolie verwendet.
Partikel
- massive leitfähige Teilchen
- massive Kunststoffteilchen, beschichtet mit leitfähigem Material
- hohle Kunststoffteilchen, die mit leitfähigem Material
Am häufigsten verwendet werden massive Graphitpartikel, Goldpartikel und vergoldete Kunststoffteilchen. Graphitpartikel sind scharf, was ein Vorteil sein kann, wenn eines der zu verbindenden Materialien eine dünne isolierende Oxidschicht aufweist. Die Nachteile sind, dass die Partikel nicht elastisch sind, was zu einem höheren Widerstand führt.
Außerdem sind Graphitpartikel hygroskopisch. Angezogene Feuchtigkeit kann sich auf die Klebstoffmatrix beeinflussen und Korrosion zwischen den Kontakten verursachen.
Da Gold nicht hygroskopisch ist, wird es manchmal gegenüber Graphit bevorzugt. Auch der Kontaktwiderstand ist geringer als bei Graphitpartikeln. Vergoldete Kunststoffpartikel sind komprimierbar, was zwei große Vorteile bietet:
Der Übergangswiderstand ist geringer, weil eine größere Oberfläche in Kontakt mit der oberen und unteren Bahn kommt. Das Teilchen wirkt außerdem wie eine Feder; eine kleine Entspannung des Klebers wird durch eine Ausdehnung des Partikels kompensiert, was zu einer besonders sicheren Verbindung führt.
leitfähige Folie
(Anisotropic
Conductive Film)
- Wenn die ACF aus drei Schichten besteht (dem Klebstoff und zwei Schutzschichten), wird eine Schicht vor dem ersten Prozessschritt abgezogen. Positionierung des Klebers und der Schutzschicht auf der Verbindungsfläche, wobei die Schutzschicht zur Thermode zeigt.
- Das Material ist vorversiegelt: Es wird einige Sekunden lang auf 80 °C erhitzt, um es mit dem Display oder der Leiterplatte zu verbinden.
- Die letzte Schutzschicht wird entfernt.
- Der Flex-connector wird auf den ACF gesetzt und ausgerichtet.
- Die Endversiegelung erfolgt bei einer Temperatur von 150-180 °C im Kleber für 10-30 Sekunden.
ACF-Flex Verbindungs-Design
Die Leiterbahnen des Flexverbinders bestehen normalerweise aus 12,5 oder 25 µm dickem, passiviertem Kupfer oder Löt- oder Zinnbeschichtungen.
Bei CrossTEQ verwenden wir vergoldete Kontakte, da sie am zuverlässigsten sind.
Die meisten Flexes haben drei Schichten, mit einer dünnen Kapton-Schutzschicht auf der Unterseite des Flexes, um die Belastung der Verbindung so gering wie möglich zu halten.
Display Design
Im Allgemeinen sollten die Kontaktflächen so klein wie möglich gehalten werden, da die Anzeigeflächen auf den Displays im Vergleich zu den Außenmaßen des Displays so groß wie möglich sein sollten. Meistens steht eine Fläche über die gesamte Länge des Displays für die Anschlüsse zur Verfügung. Die Breite des Anschlusses kann variieren. Normalerweise beträgt diese Breite 3 oder 3,5 mm.
Positionierung und finale Ausrichtung
Bei CrossTEQ nutzen wir ein Mikroskop, um die notwendige Vergrößerung und einen guten Kontrast bei der aktiven Positionierung zu erzielen. Die Ausrichtung kann an speziellen Markierungen (wie Kreuze, dicke Spuren, Rundungen usw.) auf den Bahnen selbst vorgenommen werden.
Die Ausrichtung der Teile kann auch passiv (am besten mit Referenzlöchern) erfolgen. Es ist wichtig, die Löcher so nah wie möglich an der Anzeige (Leiterplatte) zu positionieren, um eine maximale Genauigkeit zu erreichen.